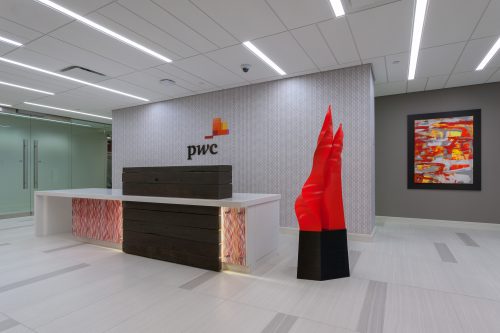
That learning includes everything I know about CAD and 3D printing that I didn’t learn from Steve Graber, who built all three of my 3D printers.
One thing that eluded me for a while is creating precision parts. This definitely came up when I created my sculpture Epic Swoon for the Columbus, Ohio, office of the professional services network PwC (PriceWaterhouseCoopers) (right).
To create the 5-1/2-foot height of the sculpture, I designed it in 2 pieces, the red sculpture itself and its black pedestal. I originally conceived the sculpture to sit flush on the pedestal, but I just couldn’t get the fit right, so I redesigned the pedestal to be complementary but not an exact fit.
I’ve learned a lot in 10 years! The precision needs to begin in CAD.
Just like I’ve learned many other things, I was playing with a design one day and, as I made a change to it, I saw it modify another part of the design. I could back out of the change, make it again, and that second change would happen again. I learned that, when I wrote a dimension (below, right) on parts, however, the changes stopped.
For example, I can make a square, but if I change one corner of it, some of the rest of the square will change as I push or pull or tug or whatever I’m going to do to it. Whereas if I give it specific dimensions, it has to stay the size I made it.
I’ve also been teaching myself how to use constraints, which help lock things where I put them. They can spin in that spot, but they won’t move from that location.
Learning how to use dimensions and constraints has helped a lot. I used them to create my sculptures Wormwood Light and Wormwood Dark and their pedestals, which are much more precise.
I still struggle with constraints. I don’t quite understand what all of them do, or when I should use which particular one, but I’m getting there.